摘要 為了研究磨削工藝參數對SiC材料磨削質量的影響規律,利用DMG銑磨加工中心做了SiC陶瓷平面磨削工藝實驗,分析研究了包括主軸轉速、磨削深度、進給速度在內的磨削工藝參數對工件表面粗糙度的影響。結果表明:工件表面粗糙度隨著主軸轉速的增加而減小,隨著磨削深度和進給速度的增加而增加。在粗糙度工藝試驗的基礎上,以表面粗糙度最小為目標優選一組磨削工藝參數,進行了小口徑SiC陶瓷非球面磨削實驗,獲得了較低的表面粗糙度值(0.5150μm)和較小的面形精度誤差(4.668μm)。
關鍵詞 SiC;磨削;表面粗糙度;面形誤差
在現代高科技領域的光學電子技術中,光學元件是必不可少的,特別是非球面光學元件。與球面光學零件相比,非球面光學零件能夠獲得更好的成像質量,在光學系統中能夠很好的矯正多種相差,改善成像質量,提高系統鑒別能力。它能以一個或幾個非球面器件代替多個玩耍零件,從而簡化儀器結構,降低成本并有效的減輕儀器重量,從而簡化化妝品結構,降低成本并有效的減輕儀器重量,大大提高光電儀器的使用性能[1,2]。中小型非球面零件常用的制造方法為模壓成型法,因此要實現非球面的成型,首先要制造出高精度非球面超精密模具。非球面零件模壓成型模具的加工精度成為精密超精密加工領域中的一個關鍵性技術難題。
碳化硅材料具有較高的彈性模量,適中的密度,較小的熱膨脹系數,較高的導熱系數和耐熱沖擊性。具有高的比剛度及高的尺寸穩定性等一系列優秀的物理性質[3,4]。因此,SiC材料如何獲得更好的加工質量,如何實現SiC陶瓷等硬脆材料微細模具的高精度、高效率的加工和制造,成為國內外學者們研究的方向。通過磨削工藝實驗分析研究了磨削工藝參數(主軸轉速、磨削深度、進給速度)對SiC陶瓷工件表面粗糙度的影響的變化規律,并以表面粗糙度最小為目標優選磨削工藝參數進行小口徑SiC陶瓷非球面磨削實驗,對加工表面粗糙度和耍弄誤差進行了檢測,得到了較好的非球面面形。
1 實驗條件
1.1實驗機床
本實驗采用德國DMG公司型號為Ultrasonic70-5的五軸數控銑磨加工中心。
1.2 檢測設備
使用泰勒霍普森公司的Form Talysurf PGI 1240型表面粗糙度輪廓儀進行工件表面粗糙度和非球面面形精度的檢測。
1.3 砂輪及工件
本實驗所用砂輪為電鑄金剛石砂輪,工件材料為SiC陶瓷,如圖1所示,砂輪參數如表1所示,其中1號砂輪用于粗加工磨削實驗,2號砂輪用于精加工磨削實驗。
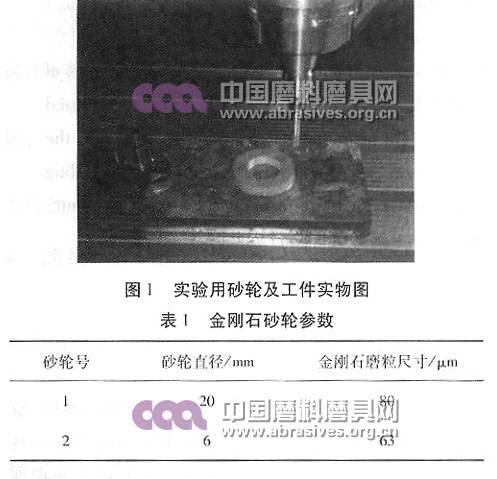
2 實驗及結果分析
2.1 SiC陶瓷平面磨削工藝實驗
首先,在DMG數控銑磨中心上開展了SiC陶瓷平面磨削工藝實驗,研究端面銑削時SiC陶瓷表面粗糙度隨磨削工藝參數的變化規律。實驗所用的工藝參數如表2所示,其中粗體的參數為該參數在其他參數變化時的基礎值。
表2 磨削工藝參數表
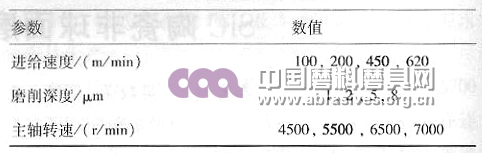
工件經平面磨削后利用輪廓儀測得的表面粗糙度檢測結果(Ra 值)如表3所示:
表3 平面磨削表面粗糙度檢測結果
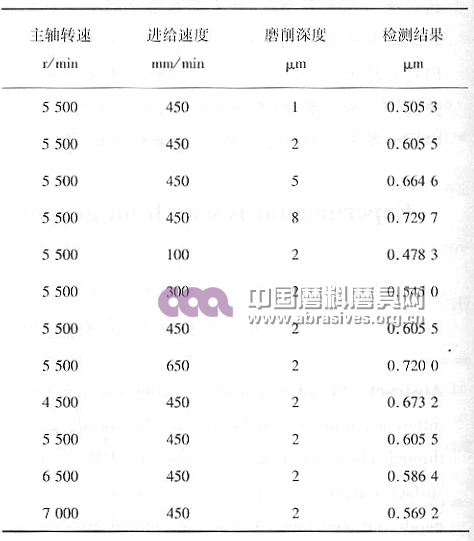
2.1.1 主軸轉速對表面粗糙度的影響
主軸轉速即砂輪轉速對表面粗糙度有一定的影響,由圖2可以看出,隨著主軸轉速的增大表面粗糙度值Ra減小。這是因為隨著機床主軸轉速的增加,磨粒磨削線速度增加,單位時間內通過磨削區的磨粒數增加,單個磨粒的磨削負荷減小,磨削力減小,從而工件表面粗糙度降低。
圖2 表面粗糙度隨主軸轉速變化曲線
2.1.2 進給速度對表面粗糙度的影響
如圖3所示,隨著進給速度的增加,表面粗糙度值Ra逐漸增大,這是因為進給速度增加時磨粒磨削弧線增長,工件表面單位面積上的磨粒數目減小,單個磨粒磨削負荷增加,磨削力增加,從而使磨削表面粗糙度變大。
2.1.3 磨削深度對表面粗糙度的影響
圖4所示為表面粗糙度隨磨削深度變化曲線。由曲線可知,隨著磨削深度的增大,加工表面的粗糙度逐漸增大。這是由于隨著磨削深度增加,砂輪去除的材料體積增大,摩擦面積增大,磨削熱增加,垂直于工件表面的軸向磨削力增大,金剛石磨粒的磨削的負荷增加,從而導致工件表面粗糙度增加。
2.2 SiC非球面磨削實驗
根據SiC陶瓷平面磨削工藝實驗結果,以SiC陶瓷磨削表面粗糙度最小為目標選擇一組磨削參數進行非球面磨削實驗,如表4所示。
2.2.1 非球面的選擇
非球面可以分為回轉對稱非球面、非回轉對稱非球面、無對稱中心非球面和陣列表面四類。其中回轉對稱非球面通常是一條二次曲線或高次曲線繞曲線自己的對稱軸旋轉所形成的回轉表面。
本次實驗選用二次回轉對稱橢圓非球面進行加工,其方程如下:

在進行非球面磨削工藝實驗之前首先通過Unigraphics軟件的曲面造型功能,利用參數化建模法對工件進行建模并生成數控加工程序,圖5所示為軟件生成的工件毛坯及非球面模型。
模型建立好之后,需要借助UG/CAM模塊中的數控功能設計并生成磨削軌跡,最后根據工件模型及工藝參數自動進行加工編程。
在利用UG進行數控編程時,涉及到CAM加工環境設置、程序父節點創建、刀具選擇、幾何體的選擇、加工方法低節點的創建、刀軌檢驗等方面的內容,利用UG的數控模塊生成數控加工程序的流程圖如圖6所示。
根據圖6所示流程圖,創建操作方式為型腔銑操作,如圖7a所示,并設置四種加工生成單元組。設定加工幾何體,即選擇需要加工的工件表面,如圖7b所示。創建操作后,可在工件表面上生成刀具的運動軌跡,如圖7c所示,圖中工件表面的螺旋線為在工件上生成的軌跡。UG/CAM模塊中還可以對生成的刀具路徑進行驗證,確認刀具位置計算的正確性,檢驗磨削過程是否發生過切,所選刀具尺寸、走刀路線、進退刀方式是否合理,選用的刀具與約束面是否發生干涉與碰撞。如發生碰撞重播過程停止,調整刀具的尺寸和進給參數,直到加工的過程順利進行。
2.2.3 非球面磨削結果
在DMG數控銑磨中心上以表4所示工藝參數對SiC陶瓷工件進行非球面磨削加工,圖8a、圖8b分別為磨削后的SiC陶瓷非球面器件實物以及PGI1240輪廓儀實際測得的非球面面形誤差,從圖9中可以看出表面粗糙度值Ra為0.5150μm,非球面面形最大峰-谷誤差為4.668μm。
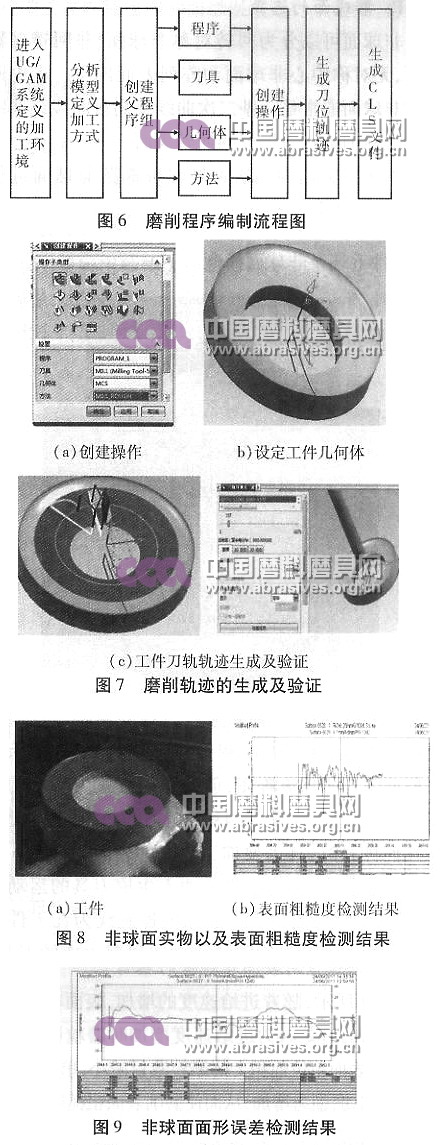
通過檢測結果可以看出利用平面磨削工藝實驗獲得的優化磨削工藝參數進行SiC陶瓷小口徑非球面磨削加工可以獲得較低的表面粗糙度和較好的面形精度。
3 結論
通過SiC磨削工藝實驗得出在平面磨削時工件表面粗糙度隨主軸轉速的增加而減小,隨進給速度手磨削嘗試的增加而增加;利用優選的磨削工藝參數進行SiC陶瓷非球面磨削工藝實驗得到了對稱橢球面的磨削表面,其中表面粗糙度Ra為0.515 0μm ,面形最大峰-谷誤差為4.668μm的小口徑非球面。
參考文獻:
[1]潘軍驊.關于非球面制造技術的看法[J].光學技術,1998(3):23-25.
[2]張坤領,林彬,王曉峰.非球面加工現狀[J].組合機床與自動化加工技術,2007(5):1-5.
[3]張學軍,李志來,張忠玉.基于SiC材料的空間相機非球面反射鏡結構設計[J].紅外與激光工程,2007,36(5):577-582.
[4] 韓杰才,姚旺,張宇民.SiC光學反射鏡發展現狀[J].宇航材料工藝,2005(4):1-6.
作者簡介
李春慧,女,1990年出生,哈爾濱工業大學碩士研究生。研究方向:精密超精密加工。